
GTAW Welding
Gas Tungsten Arc Welding (GTAW) is frequently referred to as TIG welding. TIG welding is a commonly used high quality welding process. TIG welding has become a popular choice of welding processes when high quality, precision welding is required. In TIG welding an arc is formed between a nonconsumable tungsten electrode and the metal being welded. Gas is fed through the torch to shield the electrode and molten weld pool. If filler wire is used, it is added to the weld pool separately.
- Superior quality welds
- Welds can be made with or without filler metal
- Precise control of welding variables (heat)
- Free of spatter
- Low distortion
Shielding Gases
- Argon
- Argon + Hydrogen
- Argon/Helium
Helium is generally added to increase heat input (increase welding speed or weld penetration). Hydrogen will result in cleaner looking welds and also increase heat input, however, Hydrogen may promote porosity or hydrogen cracking.
GTAW Welding Limitations
- Requires greater welder dexterity than MIG or stick welding
- Lower deposition rates
- More costly for welding thick sections
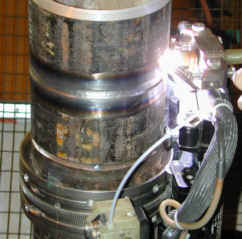
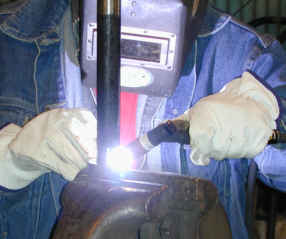
Common GTAW Welding Concerns
We can help optimize your welding process variables. Evaluate your current welding parameters and techniques. Help eliminate common welding problems and discontinuities such as those listed below:
Weld Discontinuities
- Undercutting
- Tungsten inclusions
- Porosity
- Weld metal cracks
- Heat affected zone cracks
TIG Welding Problems
- Erratic arc
- Excessive electrode consumption
- Oxidized weld deposit
- Arc wandering
- Porosity
- Difficult arc starting

MIG Welding
Gas Metal Arc Welding (GMAW) is frequently referred to as MIG welding. MIG welding is a commonly used high deposition rate welding process. Wire is continuously fed from a spool. MIG welding is therefore referred to as a semiautomatic welding process.
- All position capability
- Higher deposition rates than SMAW
- Less operator skill required
- Long welds can be made without starts and stops
- Minimal post weld cleaning is required
MIG Welding Shielding Gas
The shielding gas, forms the arc plasma, stabilizes the arc on the metal being welded, shields the arc and molten weld pool, and allows smooth transfer of metal from the weld wire to the molten weld pool. :
The primary shielding gasses used are
:
- Argon
- Argon - 1 to 5% Oxygen
- Argon - 3 to 25% CO2
- Argon/Helium
CO2 is also used in its pure form in some MIG welding processes. However, in some applications the presence of CO2 in the shielding gas may adversely affect the mechanical properties of the weld.
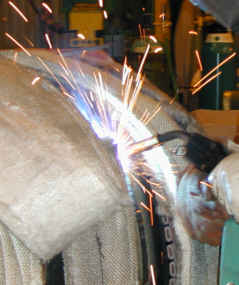
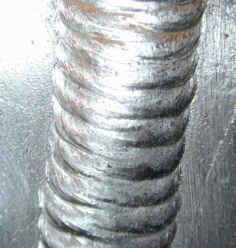
Undercut- Excessive melt-through
- Incomplete fusion
- Incomplete joint penetration
- Porosity
- Weld metal cracks
- Heat affected zone cracks
<H4>MIG Welding Problems</H4>
- Heavily oxidized weld deposit
- Irregular wire feed
- Burnback
- Porosity
- Unstable arc
- Difficult arc starting
Weld Discontinuities
Above are several different representations of weld Cracking
Below is a representation of a convex fillet weld without discontinuities